Communicating and collaborating in an electric vehicle economy
By Kari Veno, Director of Communications, Canadian Association of Recycling Industries (CARI)
Canada recycles millions of vehicles annually and the industry is robust. We continue dismantling and using shredding processes to recover valuable materials including metals and reusable parts.
“We are a resilient recycling industry accustomed to evolving and changing,” said Brian Shine, chair of the Canadian Association of Recycling Industries (CARI) and CEO of the Manitoba Corporation. “The reality is that those who transition, educate themselves, collaborate and innovate will thrive.”
Steve Fletcher, managing director of the Automotive Recyclers of Canada (ARC) agrees.
“It’s imperative that we work together as an industry to keep searching for new ways to extract and create value out of end-of-life vehicles (ELVs), to recover materials such as steel, aluminum, plastics and more, while keeping safety at the forefront.”
Both Shine and Fletcher are aligned in stating that the recycling materials industry is all about keeping up with change as new products, consumers, and channels continue to emerge.
CARI and ARC have complementary mandates and many areas of collaboration including catalytic converter theft, electric vehicle (EV) battery processing and markets, plastics from ELVs, standards for processing ELVs, and more. The organizations are supportive of one another and have many joint members including shredders and metal processors, some ELV processors, Cowan Insurance, ELV Select, Canadian Recyclers Health Benefits, and an interwoven ecosystem that has more in common than not.
As Canada continues transitioning to a circular economy that includes integrating “design for environment” principles in vehicle manufacturing to make parts and materials more recoverable and recyclable, the shift toward EVs has created an opportunity to embed these practices and respond to needs for efficiency, cost-reduction and climate change. Policy makers, consumers and markets are recognizing that recyclers are an integral part of the economy and therefore need to be part of the discussions.
When it comes to catalytic converters, there is a sustained rise in platinum group metals (PGMs) prices, which include platinum, palladium, and rhodium–the key metals in catalytic converters, hence the reason criminals are stealing these units—they’ve become a steady revenue source for ELVs. While EV recycling in Canada is still in its early stages, significant progress is being made. Most EV batteries have not yet reached the end of their usable life which is why large-scale recycling efforts are continuing to ramp up as companies develop efficient and eco-friendly methods to recover valuable materials such as lithium, cobalt and nickel. It’s hard to say exact numbers on how many EVs are currently being recycled in Canada but the infrastructure is growing in anticipation of the surge in EV batteries reaching the end of their lifecycle in the coming years.
Canada’s focus is making recycling an integral part of the EV ecosystem to ensure sustainability and reduce dependency on mining. The reuse markets for EV batteries are also in their infancy, as many stakeholders, some new to the overall automotive sector, struggle to determine how batteries can be reused. Battery state of health, fire risk, storage and logistics all have their challenges, which auto recyclers cannot tackle on their own.
“We simply do not yet have the vast experience with EVs and their new part types to understand which parts are good, bad, great, or frightening for recyclers,” said Fletcher. “It’s imperative to talk about the whole vehicle, not just the battery, as that helps to keep the economics of processing together, which helps keep EVs in the positive column.”
There are many challenges and opportunities at play, including finding new and innovative ways of sorting materials through the use of technology; research to process mixed plastics economically with programs aimed at diverting tons of plastics from landfills; costs related to acquiring the vehicle, moving the vehicle and conducting a proper environmental de-pollution; high labour costs and, of course, having the entire process remain profitable.
The auto recycling industry grew organically over 100 years ago as vehicle production and ownership grew. People were sourcing parts for their new vehicles from older models. As new makes and models appeared along with new environmental regulations, the need for a professional industry took shape. ARC defines “auto recycling” as the re-use of auto parts and the recovery of materials that have value (i.e. metals) for recycling. This also entails managing the collection and logistics to move ELVs; processing ELVs to manage the hazardous wastes that they hold; shredding depolluted hulks to access their metals; sorting those metals into ferrous and non-ferrous streams; moving those metals to be reused in the making of something new; and using the recycled materials in manufacturing.
“The circular economy for vehicles opens up more opportunities for everyone and the recycling materials industry is always up for a challenge,” said Shine. “We have expert dismantlers to recover parts and materials, expert shredders who are separating out valuable materials for recovery, suppliers, vendors and customers who are in a constant state of communication and collaboration as part of a continuous cycle with no evident beginnings or endings as we seek out our industry’s best practices.”
For more information about CARI please visit www.cari-acir.org, and to learn more about ARC, visit www.autorecyclers.ca.
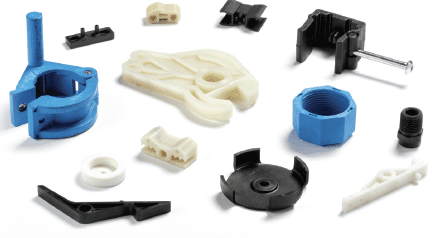